
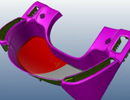
Complex Core and Cavity construction for an automotive front console
Advanced core and cavity construction using a combination of surface and solid modelling techniques. This movie also shows model validation for draft analysis, part splitting, surface extension, parting face and shut off construction.
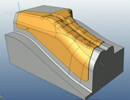
Die block construction
Construction of a die block from source CAD model using a combination of solid & surface techniques. This movie shows skin extraction, trim edits, tangential surface extension, fillet creation and boolean operations to close to a solid model.
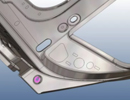
Surface Hole Filling
When preparing data for manufacture it is often necessary to fill gaps on the original model. In a solid environment it is possible to dynamically edit the model. However, with complex 3D forms this task often requires high level surfacing.
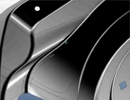
Bend relief for automotive stampings
It is often necessary to edit complex panels after running a press trial. Due to part wrinkling or material thinning causing tearing, the fillet radii are typically modified in an attempt to compensate. See how VISI has automated this process.
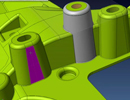
Advanced Surface Modelling
High level surface manipulation using VISI Modelling. Real life scenarios such as modifying draft angles, surface trimming, surface extension, fillet modification and hole filling with tangency and continuity validation.
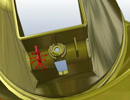
Interactive Model Editing
VISI Modelling utilises the industry standard Parasolid® kernel and provides tools to dynamically edit solid models by moving / deleting features, editing fillet radii, adding draft and moving faces all without the need to edit parametric constraints or use surface techniques.